Oil Analysis
Condition Monitoring of the insulating oil & lubricant is most important process in predictive maintenance or CBM of different machines like Gearbox, Turbines, Hydraulic Press, Transformers and different oil field equipment. The contaminated oil reduces the insulation level or a lubricant level and may lead to failure of the components of the equipment. Longer usage of oil in equipment leads to generation of gases in the oil. These gases are harmful & reduce down the insulation resistance in equipment like transformer. Which may lead to interturn, interphase short circuit or earth fault in transformer. The smooth operation of equipment like Turbine, Gear Box is depend of the lubricant. The wear & tear in the dynamic parts of these equipment can be detected by checking the lubricant. Hence, Oil Analysis or Oil Condition Monitoring is one of the major & important tool of condition monitoring & hence of Predictive Maintenance.
Oil Analysis (OA) is the sampling & laboratory analysis of the lubricant’s properties, suspended contaminants, & Wear Debris.
Basically, it is of two types, Used Oil Analysis & Wear Particle Analysis. Used Oil Analysis determines the condition & quality of the oil.
We conduct the following tests,
Lubricant Analysis – Lubricant Analysis or Lubricant Condition Monitoring is a necessary & important step in Predictive maintenance or Condition Based Maintenance. Different lubricants like Hydraulic Oil, Gear Oil, Turbine Oil, Compressor Oil, Engine Oil, etc needs to inspect for their properties periodically.
- Viscosity, ASTM D444
- TAN, ASTM D664
- Oxidation Test, ASTM D2272
- Water Content Test, ASTM D 1744
- Particle Count Testing
Transformer Oil Analysis
- Dielectric Breakdown Voltage Test, ASTM D877/D1816
- Water Content Test (PPM), ASTM D1533
- Power Factor % Testing, ASTM 924
- Interfacial Tension, Dynes/cm, ASTM D971/D2285
- Acidity, mgKOH/gm, ASTM D974
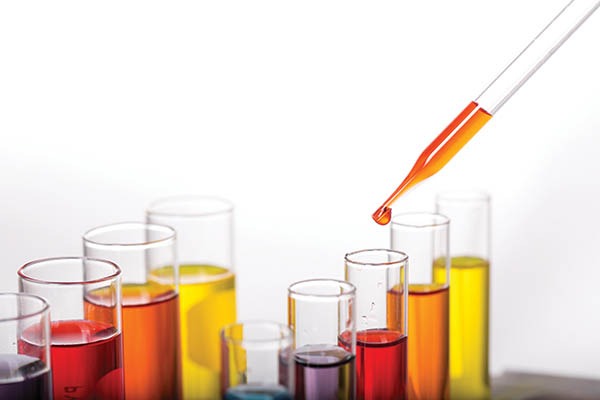
